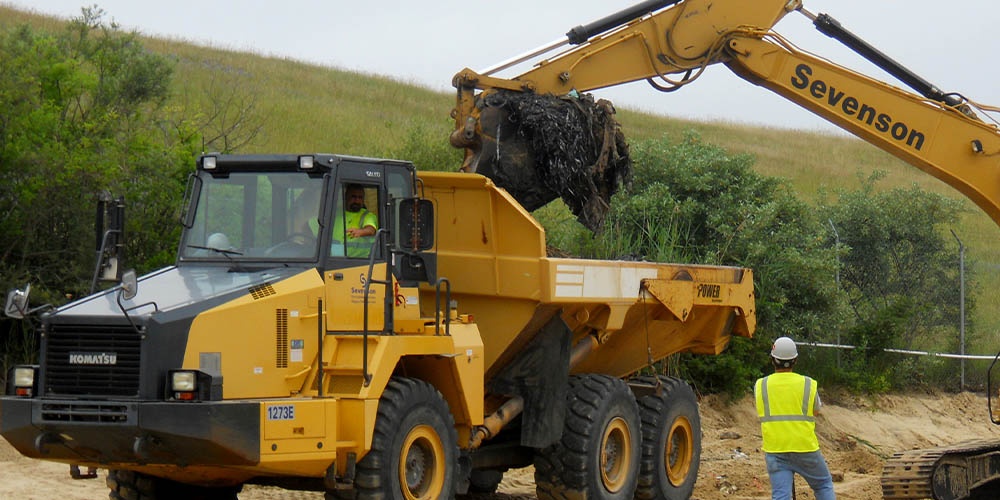
Shpack Landfill Superfund Site Remedial Action
Location | Attleboro/Norton, Massachusetts |
Contract Value | $10,500,000 |
Period of Performance | June 2013 – December 2013 |
Role | Subcontractor |
Significant Project Features
- Excavation of chemically and radiologically contaminated soils and sediments from former landfill areas and adjacent wetland
- Excavated material from several areas of the site required characterization, transportation and offsite disposal
- Dewatering/stabilization and water management was also required
- Excavation near public utility power transmission lines posed special challenges
- Constructed and created new wetlands, placed topsoil, installed plants and restored the site
Project Gallery
History & Location Details
The Shpack Landfill is located within the Town of Norton and City of Attleboro, Massachusetts. The landfill operated from 1946 until the 1970s. The landfill received domestic and industrial waste, as well as radioactive waste. Approximately 40,000 people live within a 3-mile radius of the site. Groundwater is also contaminated.
Project Description
Remedial action was performed by a group of settling responsible parties. The project was managed by Environmental Resource Management, Inc. (ERM). Sevenson was awarded the remedial action contract on a competitive bid basis.Sevenson’s work tasks were broken down into the following items:
- MOBILIZATION AND SITE PREPARATION
Upon receipt of the notice to proceed Sevenson mobilized personnel and equipment to the site to initiate site preparation activities including the setup of temporary construction trailers with electrical hook ups, internet and phone service and the installation of portable sanitary facilities. Clearing and grubbing activities were performed in the proposed staging and access/haul road locations. Sevenson also constructed material staging areas, decon pads, and access roads around the site to support soils and sediment excavation, transport and restoration operations. - EXCAVATION
Several separate areas of the Shpack Landfill required excavation. Depending on the consistency of the material as well as the results from sampling and analysis, excavated material was either stockpiled as clean for reuse as backfill; transferred to the material management area for processing or treatment prior to transportation and offsite disposal; or transferred to the dewatering area for liquids removal as well as processing and treatment prior to transportation and offsite disposal. Areas of the site which required excavation included:- Landfill Interior
Sevenson excavated backfill material and contaminated soils from the Shpack Landfill Interior area using standard excavation and earth moving equipment. Since low level radiological material, including radium and uranium, was removed under a previous U.S. Army Corps of Engineers contract, caution and stringent procedures were implemented during excavation. A health physicist was present to monitor for radiation. Every bucket was scanned prior to loading off road dumps. No radiological material above background levels was encountered. - Tongue Area
Sevenson excavated the Tongue Area to within the 10 ft buffer of an active powerline structure. Tongue Area material was dewatered and excavated on a “cell by cell” basis down to native material. Each cell was excavated and backfilled upon completion to minimize any groundwater infiltration. Sevenson laid back the slopes to ensure stable excavation conditions. A steel sheet pile wall was installed adjacent to the property line to minimize over excavation of material. Backfill was placed to final grades. Upon completion of backfill placement the Tongue Area was transitioned to National Grid so a new transmission tower and line could be installed by utility personnel. - Inner Rung
The Inner Rung area contained a highly invasive plant (Phragmites australis). Sevenson was required to remove all vegetation including Phragmites prior to the commencement of excavation. Due to its aggressive growth the Phragmites was treated with herbicides prior to removal. Once applied to the plant, two weeks was required to trans-locate the herbicide into the root system, which killed the plant. After two weeks removal could begin. Vegetation was cut flush to grade and the spoils were loaded into a material hauler for transport to the Material Management Area for off-site disposal.Sevenson excavated the Inner Rung in approximate 50-ft x 50-ft cells. The size of the cells varied dependent upon the amount of water infiltration and Sevenson’s ability to excavate, dewater, and backfill the areas on a daily basis. The cells were constructed using an aquatic dam hydraulic barrier and earthen berms. Sevenson deployed this system for each cell. Each cell was set up and dewatered in advance of excavation so work progress was not impeded. Due to high groundwater during excavation the system was constantly modified to be most effective performing the work.Sevenson filled the aqua-barriers from various sources including: the wetlands; water stored in the infiltration basin; the inner rung area sump; or water from Sevenson’s onsite water truck. When aqua-barriers were drained, the water was pumped to a new barrier or to the infiltration storage basin. Sevenson used an excavator bucket to establish a base for the barriers to ensure a sufficient seal between the ground and the barrier.To allow access of heavy equipment and materials, Sevenson utilized interlocking HDPE composite mats and timber mats to create 14-ft wide access fingers within the swamp/wetland area. For added stability a high-strength geotextile was placed beneath the mats to improve the working surface. Soils and sediment were removed with an excavator to an established grade.Initial decant of free liquids was done by stockpiling the material at the perimeter of the excavation to allow for natural draining. This reduced the amount of free liquids to be transferred to the sediment dewatering area. All stacked soils were loaded into off road haulers and transported to the sediment dewatering area prior to the completion of the work day. Inner Rung excavations were backfilled immediately as cells were completed. - ALI Landfill
Sevenson utilized steel sheeting as excavation support for soils removal from the ALI landfill area. Prior to the start of work Sevenson prepared a preliminary sheeting design for approval to allow for the safe excavation and backfill of the ALI landfill area. The bracing system included 30-ft steel sheets driven adjacent to the existing steel sheet piles. The new sheet pile wall was designed to be braced using reaction sheets, walers, and rakers. The design was modified during construction based on field conditions encountered. The shored excavation area was approximately 230 lf x 30-ft wide. The remaining ALI landfill area located outside of the shored area was open cut with the sidewalls safely sloped. Due to high water table and trapped water within the material in the excavation area, sumps and well points were installed to dewater the area prior to excavation.
- Landfill Interior
- MATERIAL MANAGEMENT
All soils and sediments removed during all excavation activities were transported to the staging and dewatering area for conditioning. Whenever possible excavated soils and sediments were transported directly to the materials management area. Materials delivered to a designated processing area were “contained” so free liquids were prevented from coming into contact with the existing stockpile of dry soils. All liquids were collected and transferred to the infiltration basin for storage and treatment. To the extent practical, wet soils were dried by blending with dry soils and/or aeration. When necessary Sevenson utilized Calciment and cement kiln dust as drying agents to achieve disposal facility moisture requirements. Dry soils were directly loaded and transferred from the active excavation to the materials management area. At the materials management area, screening and separation was done to meet disposal facility acceptance criteria. - SOIL STABILIZATION
Sevenson stabilized contaminated soil to meet disposal criteria as needed. Sevenson utilized its patented MAECTITE™ process which chemically fixates lead and other RCRA metals, effectively meeting RCRA characteristic waste guidelines and Universal Treatment Standard Land Disposal Restrictions. Sevenson stabilized the soil to meet classification as nonhazardous, as determined by USEPA Method 1311 – Toxicity Characteristic Leaching Procedure.Sevenson screened the excavated materials and removed oversized particles and debris within the Materials Management Area prior to the stabilization process. Reagent was applied to the soil. Mixing was performed using an excavator fitted with a flat-edged bucket. Mixing was done in a folding motion, which created a homogenous mix. - RESTORATION
Site restoration was initiated once final elevations were established. Restoration included the construction of permanent access roads and driving existing steel sheets to grade. The primary task required the restoration of wetlands. Sevenson worked in conjunction with its wetlands specialist. Wetlands restoration included the placement of soil amendments and plantings. Wildlife enhancement features including items such as boulders, stone piles, standing timber snags and wood debris piles were also installed. . Placement of topsoil and conservation seed mixes completed this scope of the project. - WASTE TRANSPORTATION AND DISPOSAL
Sevenson assigned an onsite transportation and disposal coordinator to assure that regulatory requirements and schedules were met. The coordinator also tracked shipments from five distinct areas of the site. Depending on waste characterization, material was sent to different disposal facilities. Transportation was done both by rail and truck. Prior to load out, waste material was prepared to meet moisture and size requirements established by each disposal facility.
Rooted in Remedial Construction
Expanded into Environmental Dredging
Start a conversation about your upcoming project
(716) 284 - 0431
© 2021 Sevenson Environmental Services -
Privacy Policy | Sitemap
2749 Lockport Road | Niagara Falls, NY 14305
P: (716) 284 - 0431 | F: (716) 284 - 7645